Bluezone Preview: Mills Focus on Versatile, Circular Fabrics
Bluezone will take place alongside Munich Fabric Start on Sept. 3-4, offering mills, trim suppliers, chemical companies, sourcing managers, designers and more the opportunity to reconnect, discover new products and soak up new knowledge.
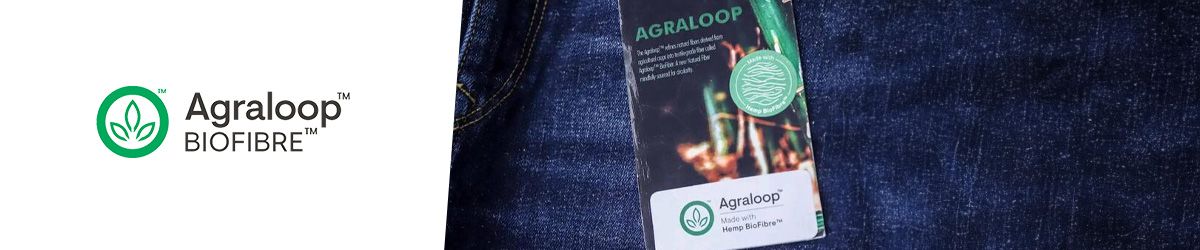
Bluezone will take place alongside Munich Fabric Start on Sept. 3-4, offering mills, trim suppliers, chemical companies, sourcing managers, designers and more the opportunity to reconnect, discover new products and soak up new knowledge.
Under the theme “Intuition,” the German trade show will feature a series of seminars exploring seasonal denim trends and key issues in the denim industry. Rivet will lead a discussion on expanding the Denim Deal recycling initiative both within Germany and internationally. Additionally, a panel including Haelixa, Tex.Tracer, Trace Momentum and Isko will delve into the topic of transparency in the denim supply chain.
Mills are planning to present Fall/Winter 2025-2026 collections focused on circular fibers and efficient ways to dye denim.
Sanko Group-owned Isko is pooling the expertise of recyclers and creatives.
At Bluezone, the Turkish mill will showcase five collections, each featuring textile-to-textile materials from Re&Up , the circular textile recycling initiative by the Sanko Group. Re&Up has pioneered an advanced process that transforms end-of-life textiles into cutting-edge materials with performance on par with virgin fibers. Leveraging Isko’s patented technologies, these materials are used to craft innovative fabrics with a wide array of unique attributes.
The five groups, made in partnership with Creative Room Italia , include: Inflexible, a range of rigid fabrics true to denim’s original heritage; Motion, a concept that combines comfort with the authentic looks of rigid fabrics; Extended, fabrics with a traditional denim aesthetic and 4-way stretch technologies; Elite, fabrics that boast softness, shine, and silky hand feels; and Momentum, a range of unique finishes, intricate constructions, colored coatings and special denim features.
The fabrics help meet the market’s demand for high-performance recycled materials, which Isko reports is expected to reach 44 million tons (more than 30 percent of the total fiber demand) by 2030.
“By relying on the Re&Up scaled solution, we are collaborating to help to close the wide recycled material gap with their prospective capacity of over 1 million tons globally,” said Keith O’Brien, Isko senior communications manager.
With Biotech fabrics, Naveena Denim Mills brings a new natural fiber refined with a waterless process to the market.
The Pakistani mill is utilizing Circular Systems’ Agraloop technology to transform agricultural crop leftovers into scalable, high-value natural fiber for new denim textiles. Biotech fabrics are made with natural fiber derived from CBD hemp crop residue and refined into a textile-grade fiber called Agraloop BioFibre.
“Crop residues are sometimes burned, left to rot, or used in low-value industrial applications,” said Berke Aydemir, Sr. GM R&D and technical sales, Naveena Denim Mills. “The Agraloop technology upgrades these residues into natural staple fiber ready to be blended and spun into yarns with other natural fiber like organic and recycled cotton.”
CBD Agraloop BioFibre uses nearly zero water. With a specialized processing technique, Aydemir said cellulose fiber from stems and leaves are purified into soft fiber bundles ready to spin into yarns. The life cycle assessment conducted by SCS Global shows that the fiber processing uses 99 percent less water, and releases 54 percent less CO2 to the atmosphere compared to conventional hemp processing.
The outcome is durable, low impact fabrics with unique natural fiber aesthetics and anti-bacterial properties. End products are also compliant with the Global Recycled Standard and Organic Blend Content Standard.
Vicunha’s F/W 25-26 collection addresses the current industry demands and consumer trends. Kürşad Çakılcıoğlu, product development and sales manager for Vicunha in Europe, said the fabrics provide a variety of “opportunities and value propositions for brands and designers seeking to stand out in a market that increasingly demands transparency, consistency and durable, high-quality products from fashion players.”
The mill’s Premium Crafts family of fabrics combine its expertise and commitment to sustainable solutions. Fabrics are crafted with special dobby designs and a blend of sustainable fibers, including ABR-certified cotton, hemp, linen, man-made cellulosic fibers, and recycled materials sourced from Vicunha’s own production facilities. Fabrics are also produced with 100 percent bio-based pigment from Nature Coatings .
Bossa is innovating how denim is dyed. At Bluezone, the Turkish mill will present fabrics made with a combination of DyStar’s EcoAdvance dyeing system with Dyeboss, a method to reduce water and energy consumption and significantly lower effluent discharge. The process produces less salt during dyeing, resulting in more consistent color, reduced shade variation, and lower salt concentrations in the effluent treatment plant.
“The Dyeboss process delivers numerous advantages, including improved oxygen stability and fewer by-products in the ETP. These benefits help us minimize our environmental footprint and support a more sustainable denim industry,” said Ozge Gul, Bossa’s sales and marketing chief. “By pioneering this approach, we set a benchmark for other mills and advance the movement towards a greener and more responsible future in denim production. As the industry evolves, it is anticipated that more mills will embrace such eco-friendly techniques, driving the shift towards a more sustainable and conscientious denim sector.”